Numerical Simulation, Modelization, Mechanical Characterization and Micro-structural Optimization of Industrial Components
Small Punch Test

Mechanical properties are the key factor when designing industrial equipment, in order to assure the safety and correct working. They depend on the material, the manufacturing process, the environment… and a great amount of material is needed to obtain standard test specimens so… what do we do when we need to analyze the mechanical behavior of an in-service component without modifying its operation? What do we do if we need to estimate the residual life of an irradiated material? How do we obtain the mechanical properties of the critical heat affected zone of a welded joint?
The Small Punch Test was born in the early 80’s, and it is one of the most important miniature test for estimating mechanical properties such as the yield strength, the ultimate tensile strength or even the fracture toughness. Now we are also researching about the possibility of estimating the level of deterioration introduced by hydrogen embrittlement.
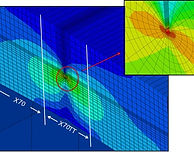
Finite Element Analysis
Finite element simulation of failure and fracture. Analytical development and numerical implementation of advanced damage models. Crack propagation analysis by means of cohesive zone models and/or the extended finite element method (X-FEM). Fracture assessment of functionally graded materials (FGMs). Finite element implementation of strain gradient plasticity theories and other advanced material models.

Shot Peening
Shot peening is a widely used cold surface treatment to improve the fatigue life in industrial metallic components, mainly in the automotive and aerospace industries. It consists in impacting the specimen surface with a stream of small high hardness spheres (Ø≤1mm; steel, glass or ceramic shots). Each impact induces a local plastic deformation on the surface layer that modifies the surface finishing, the residual stress distribution and it induces some hardening too. If the treatment is properly done, the addition of these effects can highly improve the fatigue life.
This treatment is also used to modify the surface finishing in order to improve the wear resistance, to obtain specific roughness for biological uses and to create nanoparticles in an efficient way.

Structural Integrity
SIMUMECAMAT research group has specialized in analyzing the structural integrity of any component or structure under service stresses, to ensure safe operation during its lifetime. For this we have developed a comprehensive methodology that goes from the material selection and the most appropriate treatment, stress analysis (using Finite element if necessary) and the safety factors to potential failure modes, all in accordance with the regulations in force in each case.
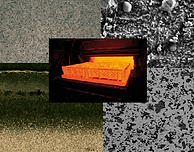
Thermal treatments
Thermal treatments are an essential stage during the fabrication of tools and industrial components. Determining the suitable parameters and sequences, among the different possibilities, results in an optimization of the lifetime of them and consequently, an economical saving.
The study of the thermal treatments is Combining the mechanical characterization with microstructural analysis techniques (optical microscopy, SEM and FEG-SEM), SIMUMECAMAT is capable of determine those thermal treatments, both global and superficial, which guarantee an increase in the service life of working tools and components.
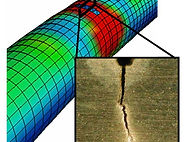
Failure assessment
The analysis of the causes of failure of any industrial component in the face of mechanical loads, thermal, oxidation, corrosion, wear, etc.., And due to the combination of all these actions is one of the active research lines of the group SIMUMECAMAT. The stresses acting on the component in question and the state of the material (forming process, heat treatment, welding, etc..) are analyzed thoroughly, which enables the determination of the causes of failure, the formulation of solutions in order to avoid subsequent damage and the actions to be taken so as to maintain a safe behavior of the industrial component.

Residual Stresses
An accurate residual stresses measurement is necessary to get a correct evaluation of the integrity of industrial components, the quality of welds or the effects of shot peening treatments. For this purpose SIMUMECAMAT uses X-ray diffraction techniques (XRD). This is carried out using a portable XStress 3000 G3R device. This equipment can measure a wide variety of steels, besides aluminium, titanium, copper, nickel, tungsten or superalloys (Inconel, incoloy,…). In order to know the subsuperficial stresses and be able to get the residual stresses profiles, it is necessary to use electro-polishing techniques that, without inducing residual stresses, can remove small layers of material.
It is important to underline the portable character of this device, the non-destructive aspect of measures as well as its quality. These features provide high versatility to these tests.